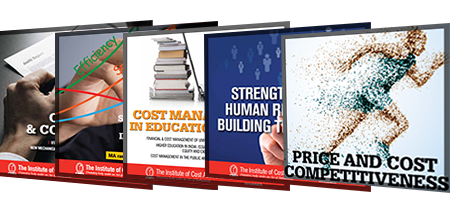
Two leading industries of the industrial revolution that played important roles in the early history of management accounting were textiles and railroads.
New trend and concepts in Management Accounting are as follows:
Just-in-time (JIT): During the last two decades of the 20th century, many companies implemented just-in-time programs designed to minimize the amount of inventory on hand. These companies identified significant benefits from reducing all types of inventories—raw materials, work-in-process, and finished goods—to the lowest possible levels.
Total quality management (TQM): Quality programs go by several names, including TQM, zero defect programs, and six sigma programs.
Theory of constraints: The theory of constraints is an operations management technique that decreases inventory levels and increase throughput in a manufacturing setting.
Lean production and the lean enterprise: In recent years, the term “lean” has been adopted by some organizations to describe the organization’s comprehensive effort to apply state-of-the-art management practices to improve quality and customer satisfaction, reduce costs and production lead-times, and increase value-creation.
Activity based costing: Activity-based costing (ABC) is a costing methodology that identifies activities in an organization and assigns the cost of each activity with resources to all products and services according to the actual consumption by each.
Activity-Based Budgeting: A method of budgeting in which the activities that incur costs in every functional area of an organization are recorded and their relationships are defined and analyzed.
Throughput accounting: It is a principle-based and simplified management accounting approach that provides managers with decision support information for enterprise profitability improvement.
Balanced scorecard: It is a strategic planning and management system that is used extensively in business and industry, government, and nonprofit organizations worldwide to align business activities to the vision and strategy of the organization, improve internal and external communications, and monitor organization.
Environmental Management Accounting: EMA is the generation and analysis of both financial and non-financial information in order to support internal environmental management processes.
Kaizen: Kaizen is the practice of continuous improvement.
Six Sigma: It can be defined as a methodology based on TQM to achieve very low defect rates.
EFQM model: It is a framework for management systems, developed by the European Foundation for Quality Management. It aims to assess performance; integrate and align existing tools, procedures and processes; introduce a way of thinking that encourages reflection and stimulates continuous improvement; and identify the key actions that are driving results.
Value chain analysis: VCA is a process where a firm identifies its primary and support activities that add value to its final product and then analyze these activities to reduce costs or increase differentiation.
Business process reengineering: BPR is the analysis and redesign of workflow within and between enterprises.
Headquarters CMA Bhawan
Kolkata Office CMA Bhawan |